Along an otherwise unremarkable roadside in Orange County, a collection of large metallic sculptures towers over an open field. These unique and mysterious art forms stand anonymous, with no signage or written explanation. But there is a clue in the 90,000-square-foot building across the road. That building houses a fine art foundry now known as UAP (formerly Urban Art Projects), and some remarkable things are happening behind its big walls.
The foundry is “a bit of a hidden gem in the Hudson Valley, and we like to keep it that way,” says Mike Price, a foundry principal who works closely with the artists who commission their work to be made there. A number of high-profile artists and galleries trust UAP artisans to not just produce every detail of their artistic vision, but also keep those projects under wraps until they are unveiled to the world.
Large sculptures like those in the field are clearly a foundry specialty. But it is also commissioned to make smaller pieces, like each of the gold-plated Oscar statuettes handed out each year at the Academy Award ceremonies in Hollywood.
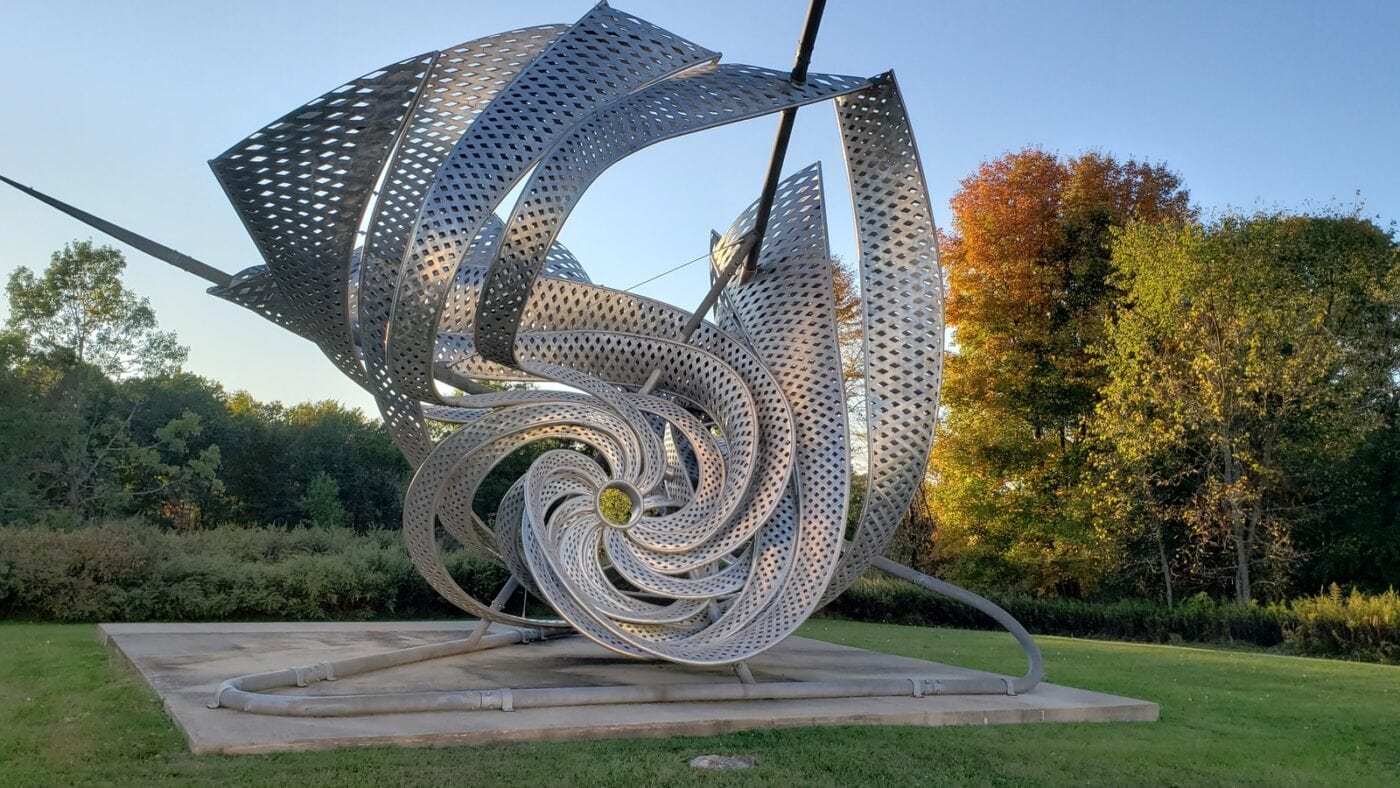
Price noted that smaller tabletop-sized pieces could take UAP workers three to four months to complete, but larger pieces can take much longer and involve more people. “It’s really a remarkable feat,” he said while peeking at a beautiful (but secret, for now) 27-foot sculpture in production. “This is one that, easily, 60 or 70 people will work on for 14 months.”
The total workforce of UAP is just over 100 people. A large percentage have a long history with the foundry at Rock Tavern. Amy Montegari, the expertise wax lead, says she’s closing in on 40 years with the foundry and its previous iterations. “I’m proud of it,” she adds.
Many of the craftspeople and their skills are connected in some way to the foundry’s origins with Dick Polich. After working in metallurgy for a brief period, Polich established various art foundries around the lower Hudson region going back to the late 1960s. Cold Spring, Peekskill, and Beacon all took their turns hosting the facility.
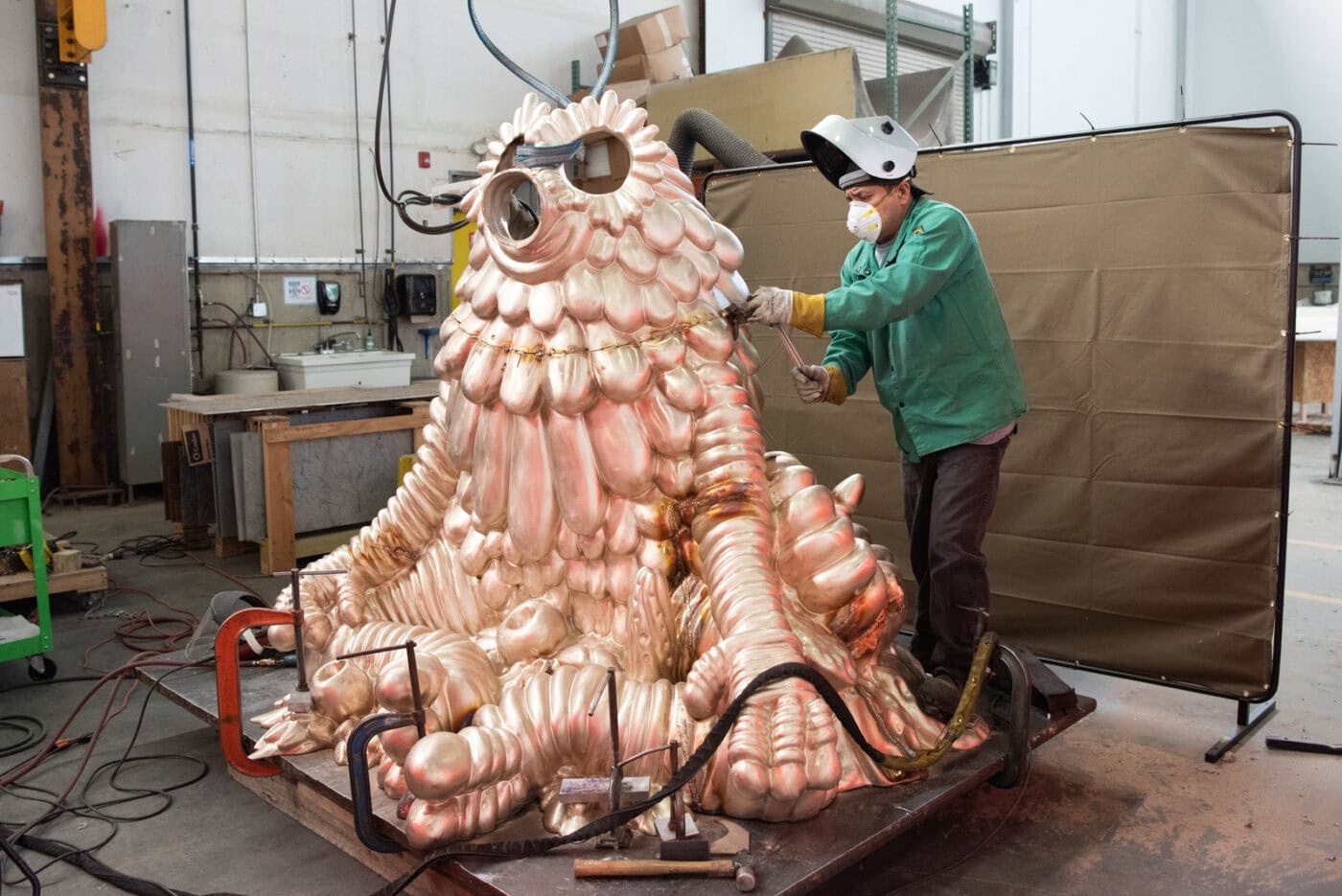
In 1996, Polich formed a partnership with artist Frank Stella and set up the foundry at the current site in Rock Tavern, N.Y., which they named Polich Tallix. As for those large metallic sculptures in the field across the road, they were pieces made by Stella that weren’t finished or intended for a gallery. In 2019, Polich and Stella sold the Rock Tavern foundry to the international art firm UAP, which carries on the legacy.
Polich died in 2022, and Stella in 2024, but the processes and techniques they developed live on today in the skilled hands of UAP’s artisan workers. “There’s a lot of knowledge that has been passed on from generation to generation,” Price says. “It’s pretty amazing to see all of the different generations that have come through here and all of the different techniques for making that you can’t find anywhere else. There’s no YouTube videos, there’s no books, there’s no classes. You literally would have to come to a place like this and learn from the masters who have been doing it for three or four decades to get that knowledge.”
UAP is known for the sand-casting process they use to create enormous molds for artwork. This is done in a space that includes three large green hoppers that stretch to the ceiling and hold 25 tons of sand each, which gets mixed with resin as it comes out to create a custom mold. “We get some molds that are 30,000-plus pounds of sand, and this allows us to pour 2,000 pounds of bronze into one mold,” Price explains. “To spend as much time as we do on a single sand mold at this scale for a piece of artwork one time is extremely unique.”
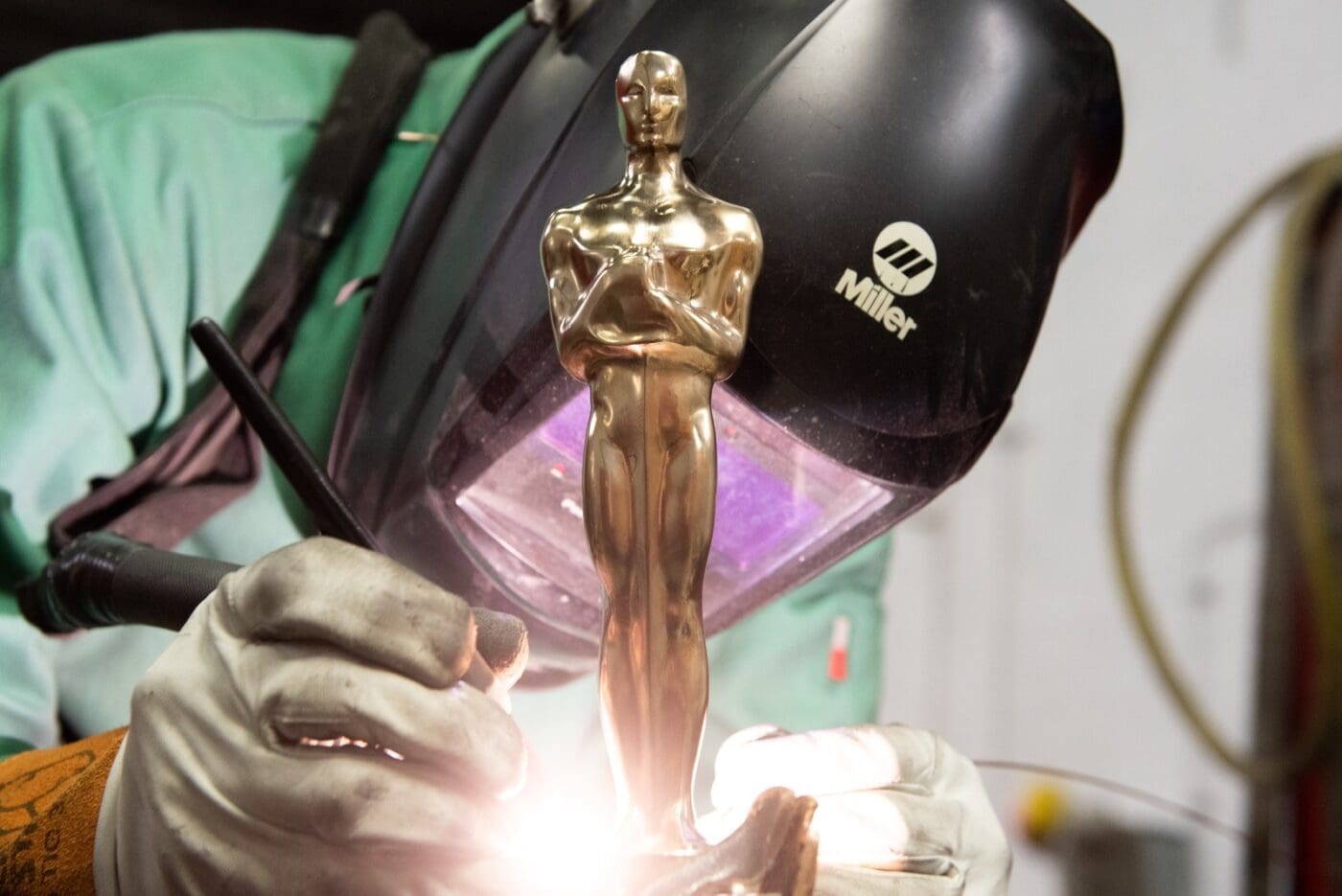
Traditional techniques such as this that have been refined over the decades are often coupled with modern innovations like computational design, digital sculpting, and 3D printing at UAP. “Our foundry has always been on the cutting edge of using technology and new processes,” Price says. This enables them to be involved with the artists from conception to completion.
Although many hands at UAP go into creating a work of art, great efforts are made to erase the fingerprints of their involvement. Artifacts of the manufacturing process like the seams, bolts, and screws that hold things together are deftly concealed, and even credit to the foundry for a sculpture is often absent by design. The goal is to remove any possible interference between the artist’s creation and the observer. “You just get to sit with the beauty of that object the way the artist intended,” Price explains. “And that’s something we really strive for, to really make sure that we are invisible.”
Despite this invisible involvement with some of the most recognizable sculptures, and despite the nondescript building where those pieces are discretely built in Rock Tavern, UAP still makes waves in the Hudson Valley arts scene. It’s no surprise that they have a strong relationship with the Storm King Art Center and have produced works on display there such as New York artist Sara Sze’s “Fallen Sky,” a representation of earth’s fragility and flux that was installed in 2021. They also support local galleries, art initiatives, and events like the recently launched Upstate Art Weekend. And they maintain a few residency studios onsite at the foundry, primarily for younger artists who don’t have gallery representation.
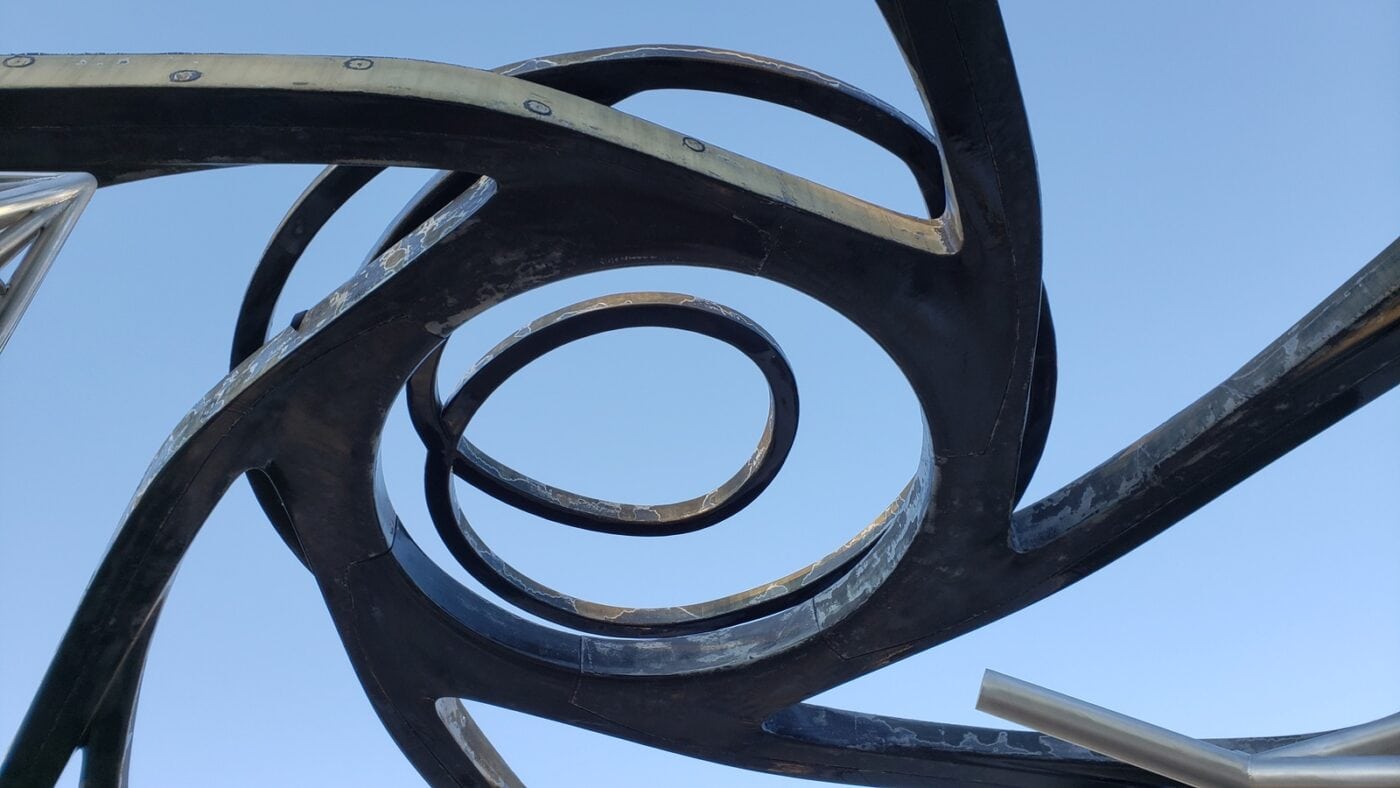
“The community impact of the foundry in Rock Tavern cannot be separated from the individuals who have decided to make it so,” says Todd Hulet, executive director of the Orange County New York Arts Council, which partners with UAP. “Dick Polich spent decades not only employing hundreds of artisans but fostering and mentoring their craft in the process. Following in his legacy, UAP has made the intentional commitment to do the same,” he says.
All of this continues to solidify UAP’s status as one of the most outstanding foundries in the art world. Despite some of its high-profile work, it remains a hidden gemstone in the Hudson Valley.